The Bunker
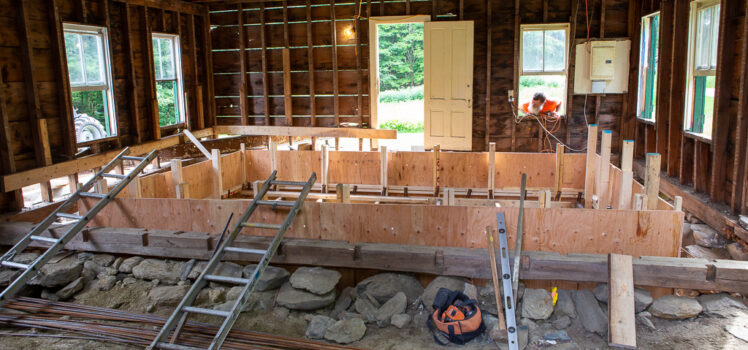
This is where our builder’s experience and creativity shine. Encasing the cellar stone walls in cement will serve multiple mission-critical purposes: it will halt the degradation of the stone wall integrity, deter moisture from re-entering the cellar, and provide a solid foundation for leveling the house structure. If we can successfully pull this off it will be an important milestone, one that many said could not be done and was a waste of time to try.
The strength of a building lies in its foundation.
Whether sage advice or biblical reference, we’ve heard a lot about how important a solid foundation is to saving this old house. While the cellar is only under a little more than half the footprint of the house, getting a substantial concrete structure in place will establish the level for all four corners of the house.
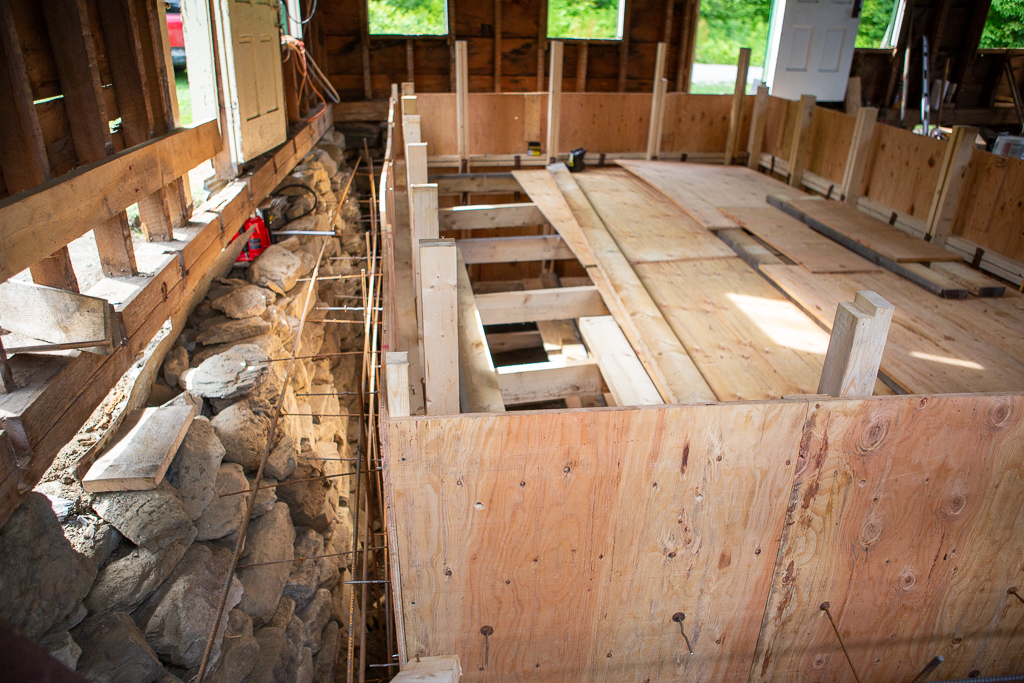
Building the form takes a lot of 2x4s of varying lengths along with almost two dozen sheets of plywood, assorted planks, 20-foot long pieces of rebar cut to length, connecting pins, tie wires, and a host of related tools. We learn a new vocabulary with terms such as waler and strongback. We plan to reuse all the lumber, so take care to minimize cutting.
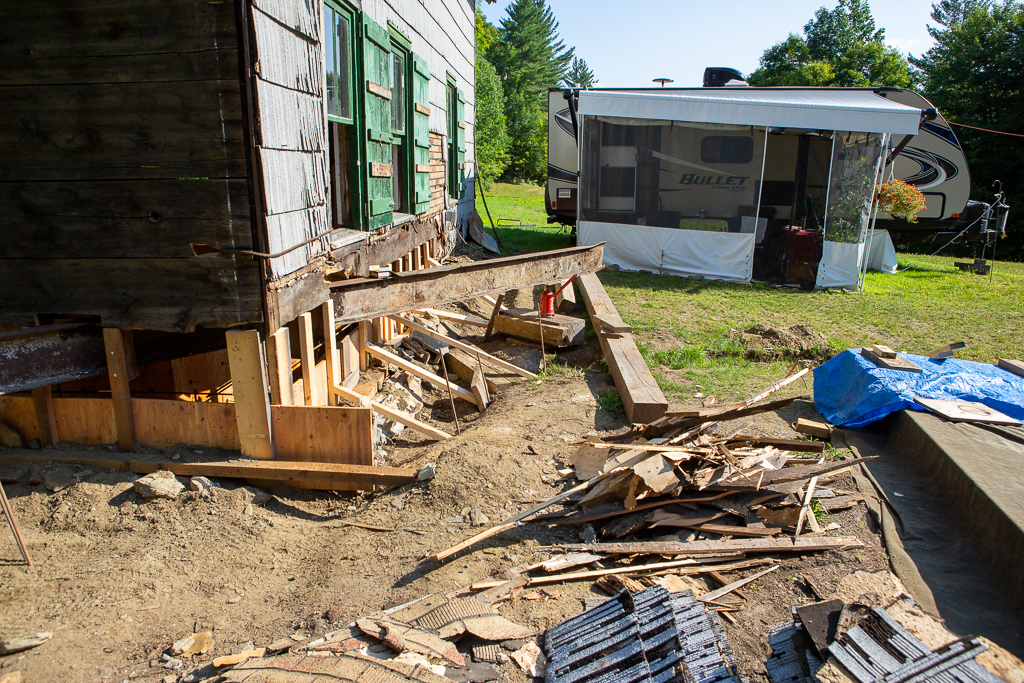
Since the newly poured concrete will serve as a foundation, the entire house on the cellar end is lifted so it can be set down on the top of new cellar walls. We knew there was some rot in the sill beams, but lifting the house reveals the sad news that all of them must be replaced. Carpenter ants have essentially hollowed out the beams and the wood crumbles when exposed.
We start building the form in late July and by the first week in August we’re ready for concrete. Due to the irregularity of the stone walls, it’s impossible to estimate the amount of concrete we will need. A friend of our builder who has built concrete foundations, walls, basements, etc. stops by to help determine how much concrete we should order. He says the form is solid and he can’t imagine what more could be done to hold back the extreme pressure created by the yards of concrete, but we’re still nervous. He also tells us about a job he worked once where a one-sided form like ours popped up unexpectedly when the concrete was poured which allowed it to run beneath the bottom of the form and halt the project. The next day we add vertical boards and secure the ends to the remaining second floor joists.
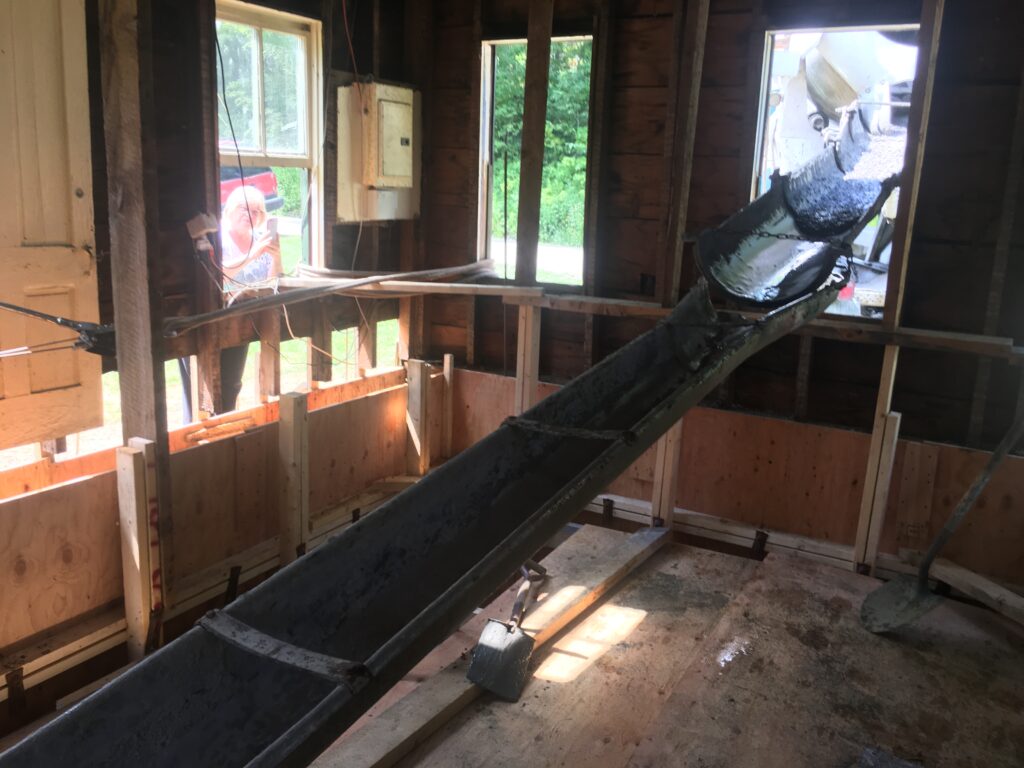
We have only two concrete companies from which to choose. We estimate that the pour will take 21 to 22 yards and we order three truck loads. The first truck will have a full load of 10 yards, the second truck will be loaded with eight yards, and the last truck will have four yards. We put the third truck on standby in case we need it without committing to purchase the load.
We’re completely stressed waiting for the first truck to appear. We’re quietly thinking about what we’ll do if there’s a blow out. The first driver arrives without a sufficient supply of water so there’s nothing to loosen the stiff concrete coming down the chute which delays pouring and creates a mess from overflows. The second truck arrives early and when that driver schools the first driver, things get back on track. Near the end of the pour from the second truck we call off the third truck. Based on what’s left in the second truck, we think about 17 yards filled the gaps between form and stone. Today we created a veritable bunker. Tomorrow we tear down the forms.