Slabs
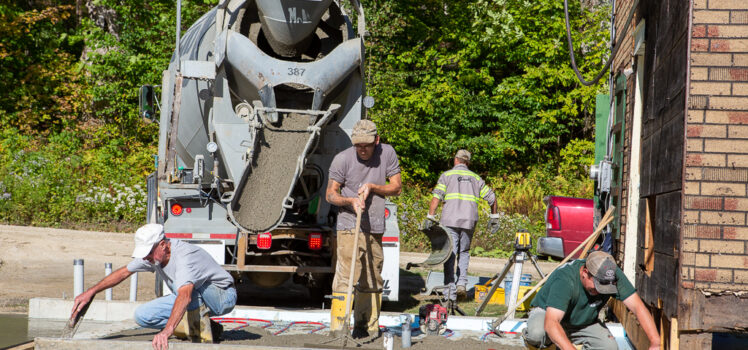
In contrast to the work on frost walls and excavation, pouring the slabs went quickly. Unlike the frost walls, the slabs were fibrecrete, a concrete alternative made up of concrete fibers, glue, and recycled byproducts. It is designed to be stronger than concrete, but lighter.
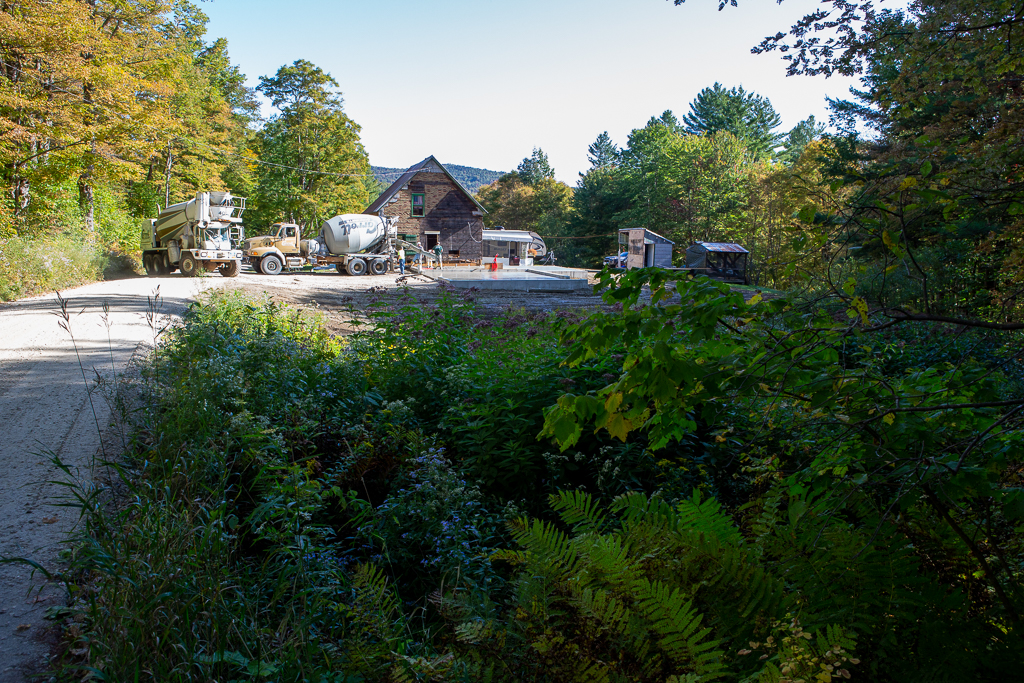
The concrete truck and foundation crews work quickly. As with the frost wall pours, they communicate visually with non-verbal gestures and an occasional whistle or two. They shape the garage slab to slope slightly to the center drain. It’s a good thing we didn’t skimp on staples to affix radiant tubing to the foam insulation because the pour is not a delicate flow. Everyone leaves after a relatively short period of time, vowing to return for finishing.
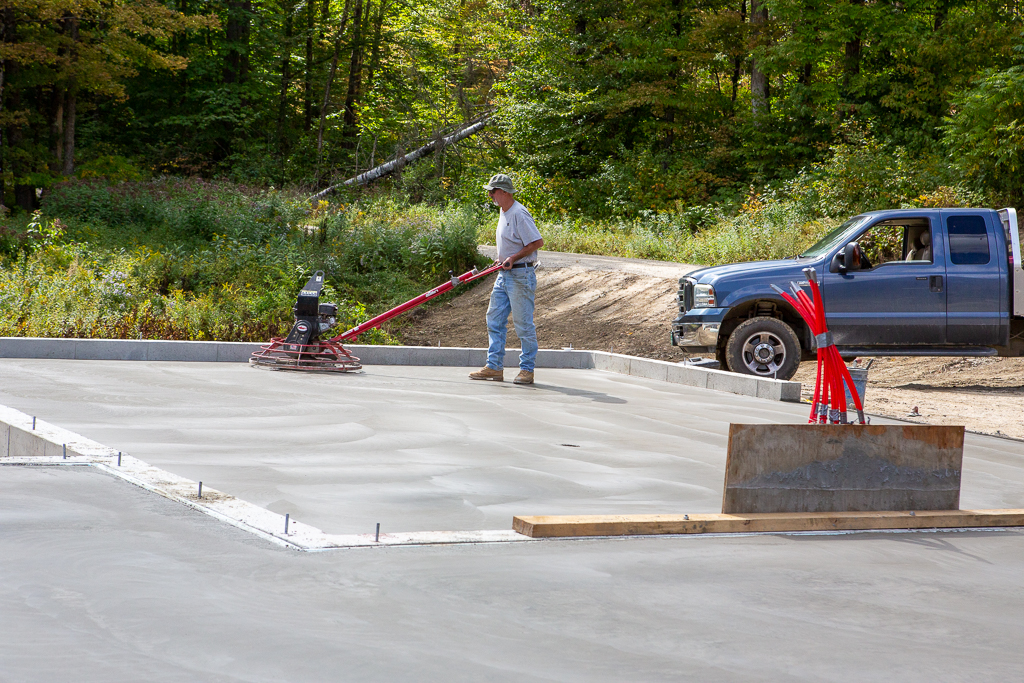
A few hours later, two members of the foundation crew return and unload motorized finishers. They start off gingerly walking behind the power trowels, smoothing over their tracks. Each wave of smoothing and troweling is separated by an hour or so of wait time as the surface hardens.
By the end of the day, the structural icing is on the foundation cake and the crew chief declares the job finished. We’re advised to stay off of the surface for at least a week. We aren’t sure if the builder can get started on framing. The weather has already started getting cooler, especially in the morning. Getting the foundation in place was an unexpected accomplishment, a project we had planned to complete next year.
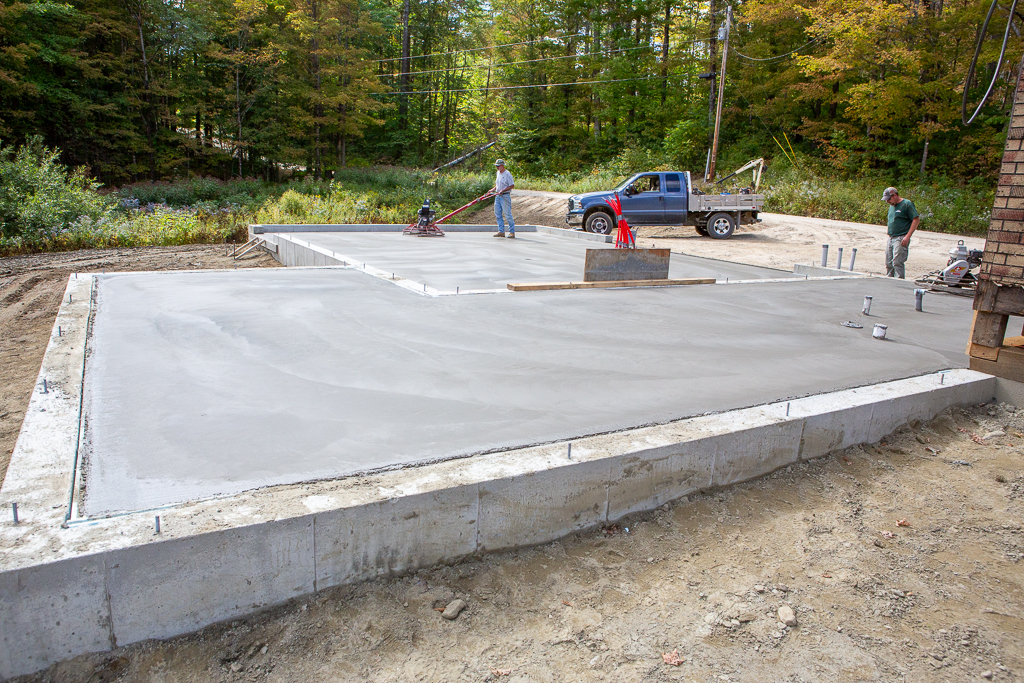
We begin gathering feedback on how to protect the slab in a cold Vermont winter. It can’t be good for ice and snow to settle in on the surface. Recommendations range from covering with straw or a tarp to doing nothing. We’ll need a slab protection plan so the expensive foundation will weather the months before we can return in the spring next year.