Earthquake Maker
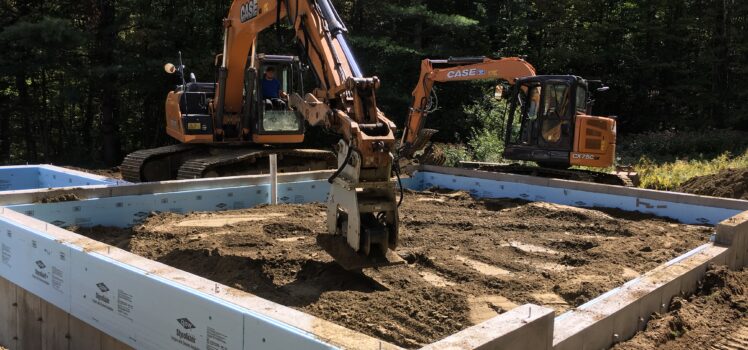
Filling in the frost walls makes the site get smaller. The excavator crew uses three machines: small, medium, and large. A lot is getting done in a relatively short, but expensive, period of time.
- Backfill the areas that will serve as foundations for the new structures.
- Install and bury a permanent water line connecting the rustic spring well with the house.
- Run three lines of conduit between the garage and the last power pole located on the other side of the road so we can eliminate the aerial wires for electricity and internet.
- Regrade the area surrounding the foundations so that heavy concrete trucks can maneuver into position for pouring slabs.
- Install a proper driveway using hard pack material much like the town road.
The filling in process proceeds rapidly with existing excavated material and 10-wheeler dump truck loads of a sandy material. The earthquake maker attachment to the large excavator (see photo above) is used to compact the area where the slab will be poured. We can hear and feel it anywhere on the property. It’s heavy which when combined with pressure from the excavator allows us to see incremental progress. This is definitely a serious piece of equipment.
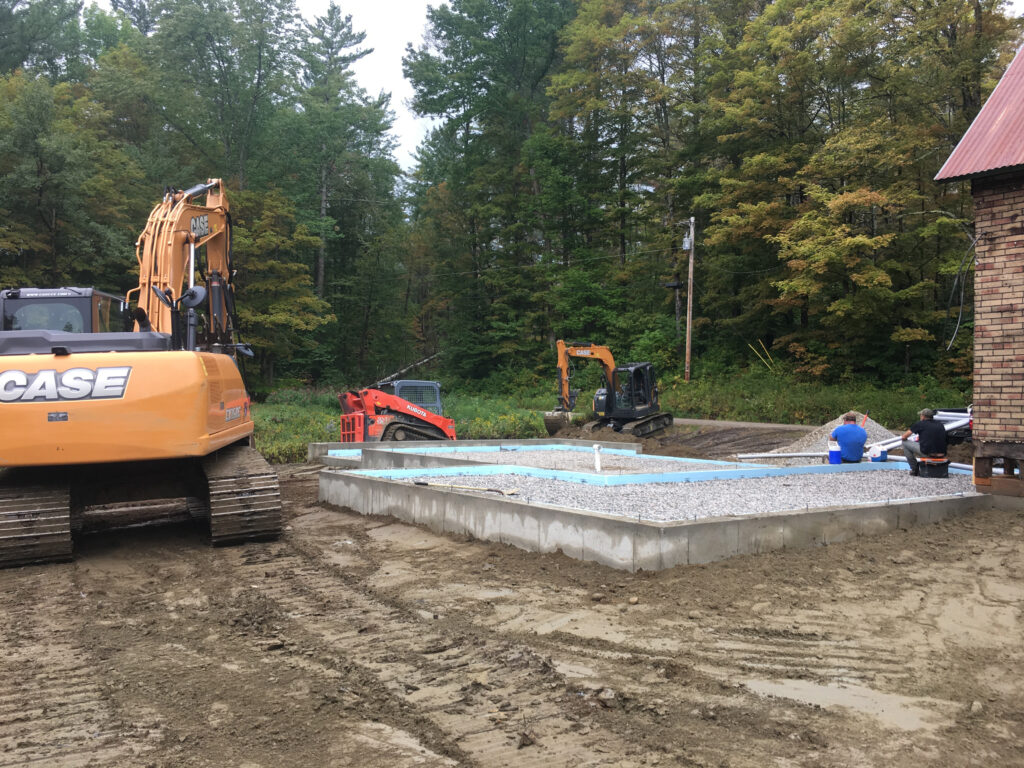
After backfilling and compacting, loads of gravel are delivered and added to the slab cavities. We ask them to leave two inches to accommodate foam board and radiant tubing.
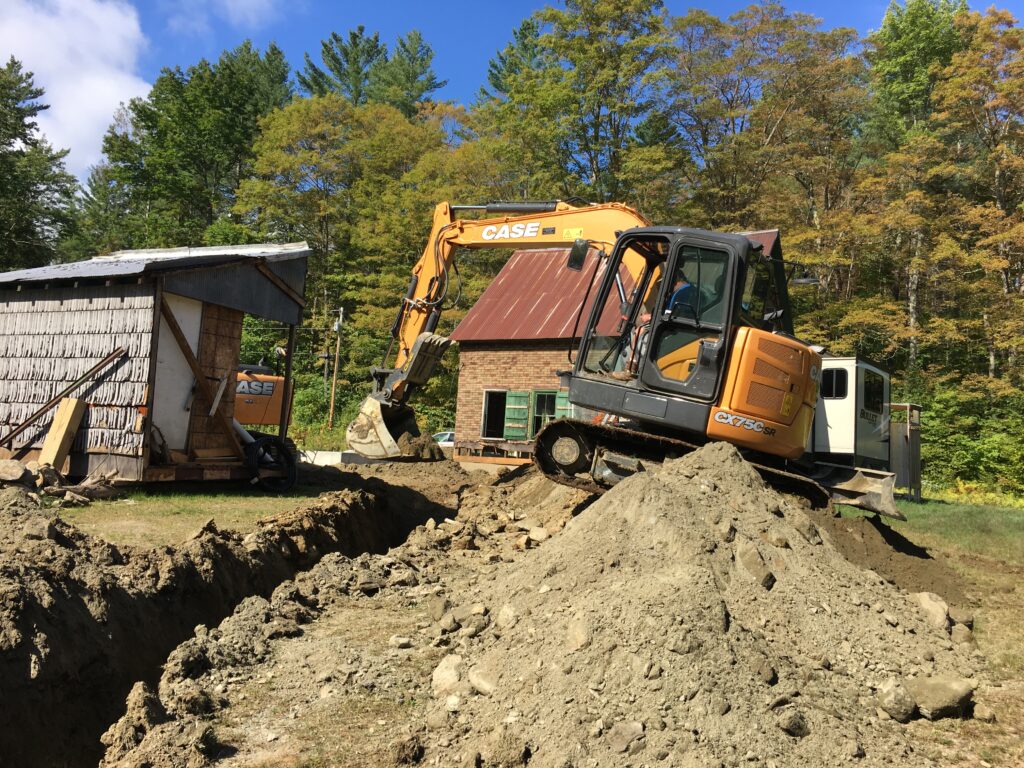
Once the foundation area is secure, the excavators turn their attention to digging a trench, about 120-feet long, from the house to the existing rustic spring well. They have to squeeze machinery around existing obstacles such as the RV and shed. In the process, they manage to clip the existing water line from the rustic spring well to the RV. We quickly unplug the pump, repair the line, and get back to work.
As work progresses we are summoned to the trench, about 30 feet from the well. Work has stopped and everyone is looking down into the trench. No one says anything, so we stand there and look into the trench to see a considerable flow of water, downhill of course.
“Did you guys hit our water line again?” We ask.
“Nope, we found an underground spring.” reports the crew chief.
We learned years ago to listen to locals. In the beginning, they were not quick to offer advice. In hindsight, that’s likely because they make more money executing the mistaken plans of well-intentioned homeowners who think they know what they’re doing. Since we clearly do not know what we’re doing, we ask for advice. What do we do with this information?
After a pregnant pause, the crew chief replies,”Well, you’ve always asked me what I’d do if it were my property. ” Yes, we have, and the advice has been valuable.
“I’d put in the new well now and not wait until next year. I’ve got a full crew here, along with all the machinery and gravel. All we need are tiles, but I can get those here after lunch,” he assures us, then adds, “I’ll make it worth your while.”
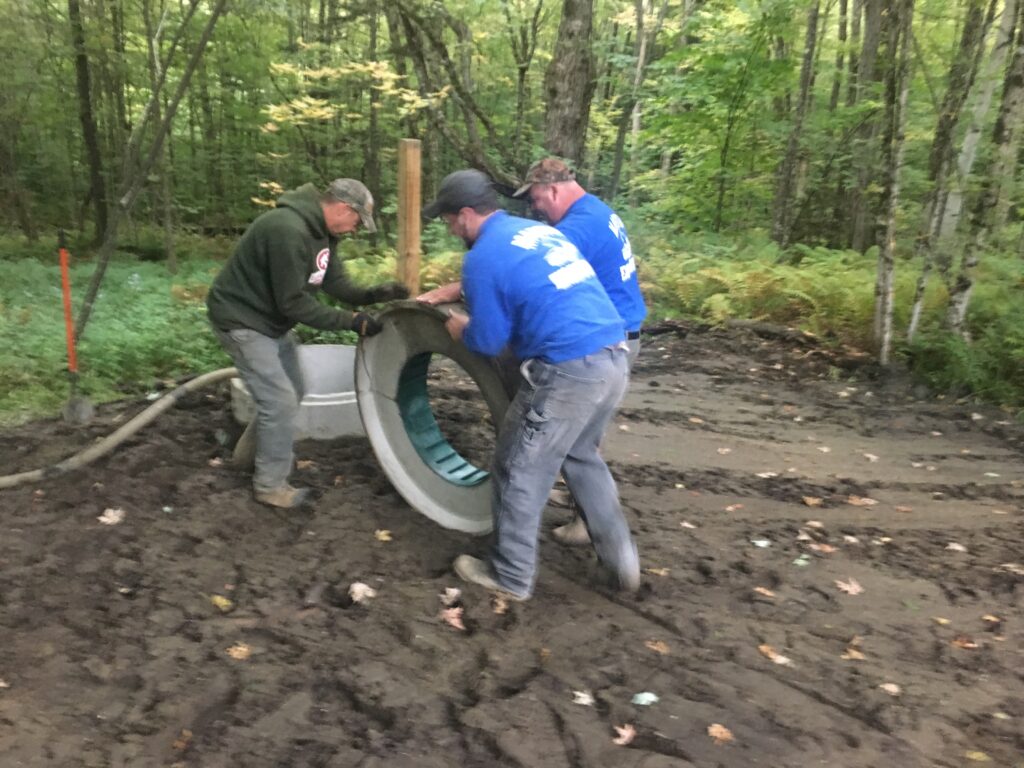
We agree to the new proper spring well and the digging continues in earnest. Before we know it, a trailer loaded with sections of concrete pipe, aka tiles, arrives and are stacked on top of each other vertically in a deep muddy hole.
This is the first piece of good news we’ve received while working on this project. The budget was steep for a new well, so steep we had planned to make do with the small, shallow rustic spring well until we were in a better financial place. In just a few hours, we went from having less than 150 gallons of mostly surface water to more than 1,000 gallons of mostly underground spring water. The icing on the cake? This is September when many of the ponds and wells in the area are dry or down significantly. Finding a viable source of water at this time of the year promises that we’ll have a reliable well in the future.
The next day we run errands while the crew buries the conduit from the side of the new garage to the power pole. When we return to the job site, there’s a proper driveway waiting for us. The crew promises to return for a final dress grading in the summer next year. We still have a lot of deliveries and concrete trucks that will be driving around on the “yard.”
While it is gratifying to get some of these major items checked off the project infrastructure list, with most of it underground we conclude there’s little to show for all the time and money. We still have insulation, radiant tubing, and slabs to go. Great, more stuff that’s mostly underfoot.